Content
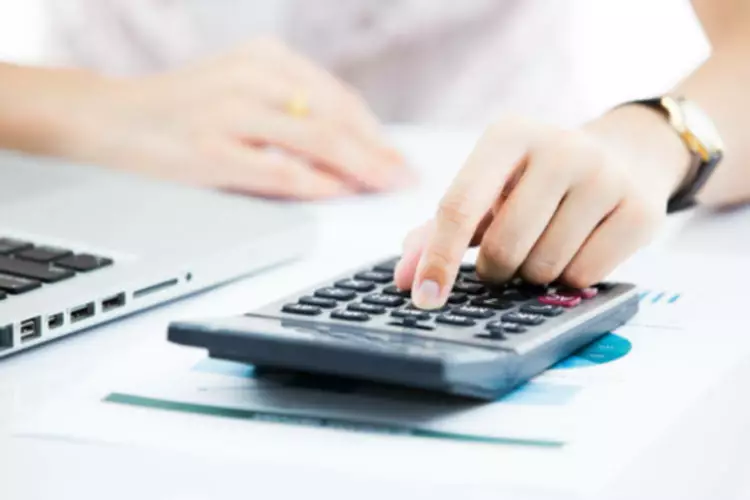
It’s a measure of the true cost of a manufactured item, including labor and overhead. Thus, the total cost of goods manufactured for the period would be $265,000 ($100,000 + $50,000 + $125,000 + $65,000 – $75,000). This means that Steelcase was able to finish $265,000 worth of furniture during the period and move this merchandise from the work cost of goods manufactured in process account to the finished goods account by the end of the period. The cost of goods manufactured is covered in detail in a cost accounting course. In addition, AccountingCoach PRO includes a form for preparing a schedule of the Cost of Goods Manufactured. Manually managing wholesale inventory for your business is no easy feat.
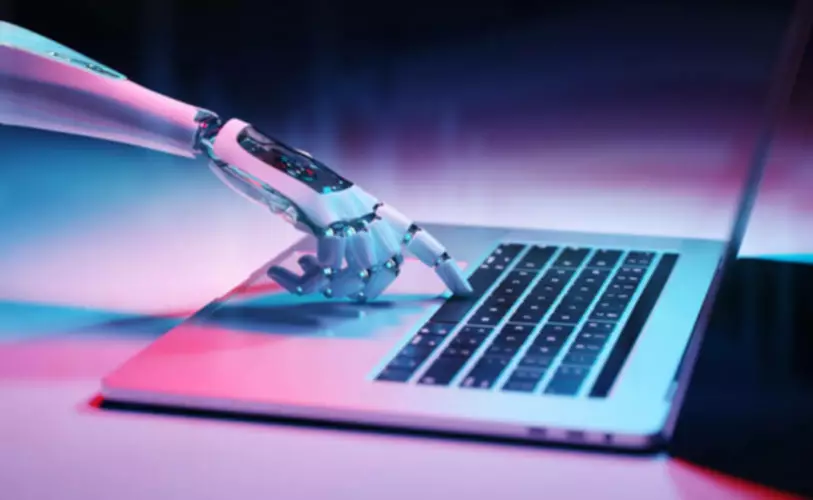
The best approach to examining the cost of goods manufactured is to disaggregate it into its component parts and examine them on a trend line. By doing so, you can determine the types of costs that a company is incurring over time to produce a certain mix and quantity of goods. Cost of goods manufactured is the total of all the raw materials, direct labor, and allocated manufacturing overhead used during the period to create completed products. The gears and casings they buy from their supplier are the direct raw materials the employees will convert into clocks.
What is the prime cost method?
All it’s doing is assigning a value to every unit produced based on raw materials, labor, and overhead. The total labor and all manufacturing costs other than direct labor are known as conversion costs. These include indirect labor, quality control inspection, indirect materials, machine setups, factory supervision etc. The cost of goods manufactured includes all manufacturing overhead costs incurred during the accounting period. The accounts from which overhead is compiled are set by accounting policy.
Examples of pure service companies include accounting firms, law offices, real estate appraisers, business consultants, professional dancers, etc. Even though all of these industries have business expenses and normally spend money to provide their services, they do not list COGS. Instead, they have what is called "cost of services," which does not count towards a COGS deduction. LIFO is where the latest goods added to the inventory are sold first. During periods of rising prices, goods with higher costs are sold first, leading to a higher COGS amount.
How Do You Calculate Cost of Goods Sold (COGS)?
For worthless inventory, you must provide evidence that it was destroyed. For obsolete (out of date) inventory, you must also show evidence of the decrease in value. Once you have gathered the relevant information, you can calculate the cost of goods sold. To use the inventory cost method, you will need to find the value of your inventory. The IRS allows several different methods (FIFO or LIFO, for example), depending on the type of inventory. The IRS has detailed rules for which identification method you can use and when you can make changes to your inventory cost method.
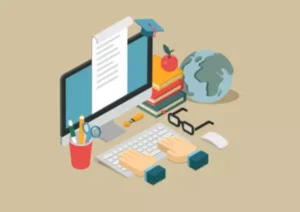
As savvy business owners and supply chain management enthusiasts, it's crucial to understand the ins and outs of inventory management, and finished goods inventory is no exception. In this comprehensive blog, we'll dive deep into the intricacies of the finished goods inventory formula, revealing the secrets behind calculating your stock like a pro. All of the above can become exponentially more complicated when volumes and product lines increase.
Cost of goods manufactured VS total manufacturing cost VS cost of goods sold
Manufacturing companies have accounting variables that are specific to manufacturing settings. These include work-in-progress inventory, raw materials used, labor costs for production, and manufacturing overhead. These can be used to calculate the costs that are specific to the manufacturing of goods. In COGM, the computation of factory overheads, which are the indirect production expenses, including rent, utilities, and depreciation, includes indirect materials.
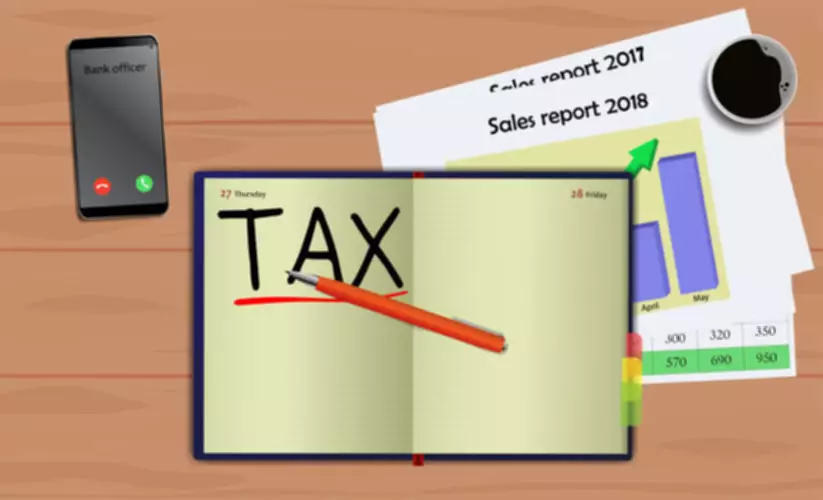
Finished goods inventory becomes finished goods inventory by first being the other two types of manufacturing inventory. One manufacturer's finished goods inventory may be a retailer's merchandise inventory, dropshipping inventory, or another manufacturer's raw material or component. The destination of these finished goods determines their classification after completion. Also excluded from COGS are the costs for products that remain unsold at the end of a given period. Instead, these are reflected in the inventory on hand at the end of the period.
Calculate the Cost of Goods Manufactured (COGM) to total your manufacturing cost. The Cost Of Goods Manufactured (COGM) formula is a powerful tool to help managers analyze their company's production costs. Businesses use COGM to measure the direct expenses of manufacturing goods and services. This information is essential for companies to stay competitive in today's marketplace.
- Direct and indirect materials may be included in the raw materials inventory.
- COGM stands for “cost of goods manufactured” and represents the total costs incurred throughout the process of creating a finished product that can be sold to customers.
- And once you have finished goods inventory numbers you’re confident in, you can start optimizing it.
- Total costs to create products are divided by total units created over the entire period.
- Working closely with manufacturers on case studies and peering deeply into a plethora of manufacturing topics, Mattias always makes sure his writing is insightful and well-informed.
- Making sense of COGM and having efficient systems to measure and track them is key to your survival as a manufacturing business.
- As the name suggests, the COGM calculates the total manufacturing cost incurred on a product that has been manufactured and is ready to be sold.
- Overhead costs can be harder to track because they may not be as directly related to the production process as materials or labor are.
Read about the ins and outs of the wholesale inventory management process and learn about the tools that can make your inventory control woes a thing of the past. For example, if you purchase $1000 worth of raw materials but don’t sell them until six months later, you would recognize that $1000 expense in your books as cost of goods sold. The cost of goods manufactured (COGM) is an important metric, especially for manufacturing businesses, because it can affect profitability, which is the ultimate goal of any business. COGM is assigned to units in production and is inclusive of WIP and finished goods not yet sold, whereas COGS is only recognized when the inventory in question is actually sold to a customer.
Determining Direct Materials Used
Investors looking through a company’s financial statements can spot unscrupulous inventory accounting by checking for inventory buildup, such as inventory rising faster than revenue or total assets reported. It helps calculate the cost of goods sold, which is used to calculate gross profit. In summary, COGM links to COGS because COGS is the sum of COGM and the change in finished goods inventory during a given period. Use this information to evaluate the cost and profitability of producing and selling a product and make cost management and resource allocation decisions.
Examples of these accounts are manufacturing rent, manufacturing depreciation, manufacturing supervisory compensation, quality control compensation, utilities, repairs and maintenance, and production supplies. Manufacturing costs refer to any costs incurred during the process of manufacturing a finished product and include the 1) cost of raw materials, 2) direct labor, and 3) overhead costs. Any other costs incurred for the manufacturing process that is not part of direct materials and direct labor will be part of manufacturing overheads. It’s easy to calculate direct labor costs for a manufacturing facility.
For a business to calculate the actual amount of direct materials that were used for production, it is essential to take into account the T-Account for the raw materials inventory. Cost of goods manufactured (COGM) is a term used in accounting to describe the total cost of manufacturing goods during a specified period. It determines the inventory cost at the end of an accounting period and ultimately calculates a company's gross profit.